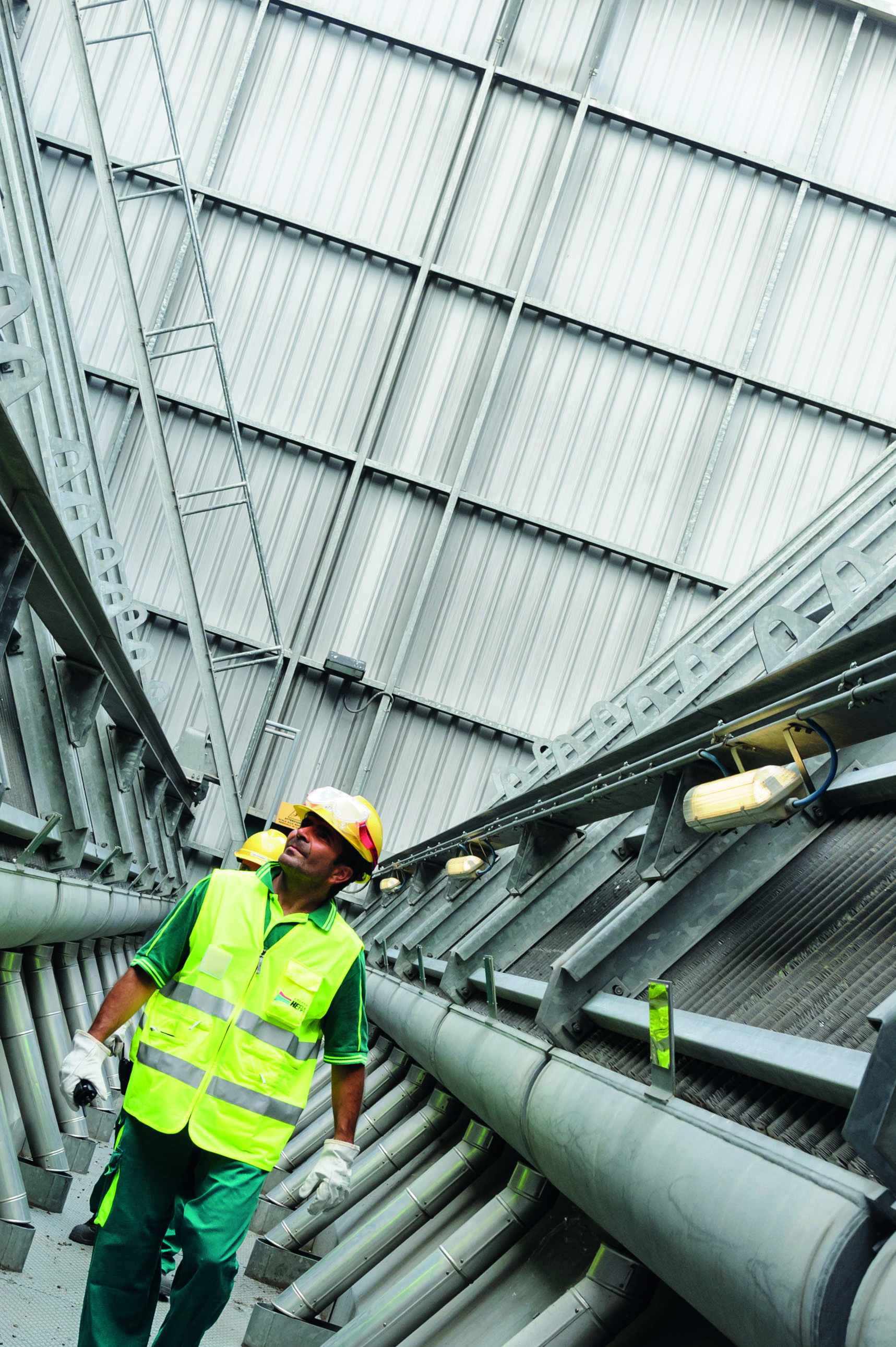
Un grande network europeo che guarda al futuro
Grazie alla nostra dotazione impiantistica unica in Italia composta da 95 impianti e un network di operatori europei qualificati arriviamo ovunque serva, affinché ogni rifiuto trovi la sua strada e diventi valore. Lavoriamo minimizzando il ricorso alla discarica e investiamo in progetti innovativi e tecnologie all'avanguardia che permettano di massimizzare ancora di più il recupero dei rifiuti.
Scopri tutti i documenti per accedere ai nostri impianti
Una gestione sicura e trasparente
I nostri impianti sono certificati, tecnologici e allinati alle BAT Best available techniques europee: le migliori soluzioni tecniche impiantistiche, gestionali e di controllo in grado di garantire un elevato livello di protezione dell'ambiente attraverso, bassi livelli di emissioni di inquinanti e l'ottimizzazione delle materie prime utilizzate nel processo. Gestiamo i siti con la massima sicurezza e trasparenza monitorando e pubblicando costantemente i dati relativi alle loro emissioni.
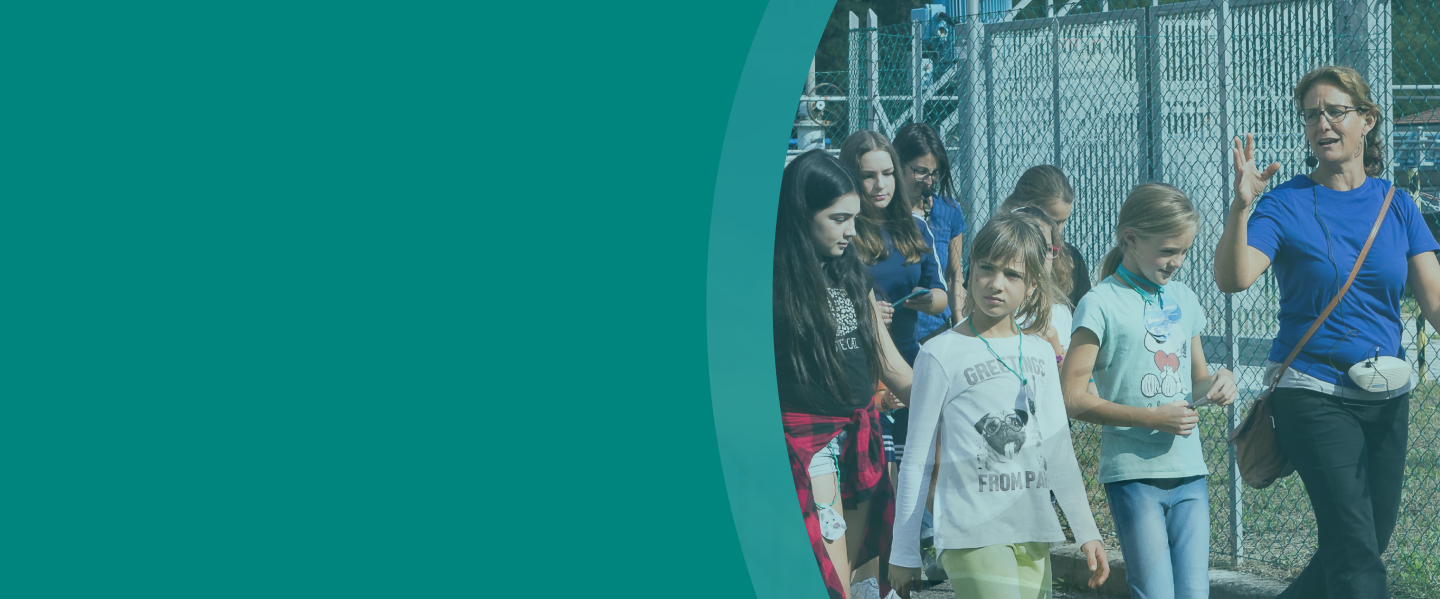
Sei interessato a visitare uno dei nostri impianti?
Herambiente apre gli impianti a chiunque desideri vedere quale sia il percorso dei rifiuti: prenota on line la tua visita guidata.